raw material optimizer
The solution for substantial cost savings and CO2 reduction
Using the raw material optimizer enables steelmakers to make steel making more effecient.
The software solution, which is easy and quick to implement, supports operators in realizing cost-optimized raw material inputs along the entire process route.
Moreover, significant CO2 reductions can be achieved, thus, making a valuable contribution to protecting the climate.
Let's start a joint project towards CO2 and cost reduction?
Many steel producers (especially stainless steel producers) are not aware of the enormous potential of reducing raw material costs as well as CO2 emissions.
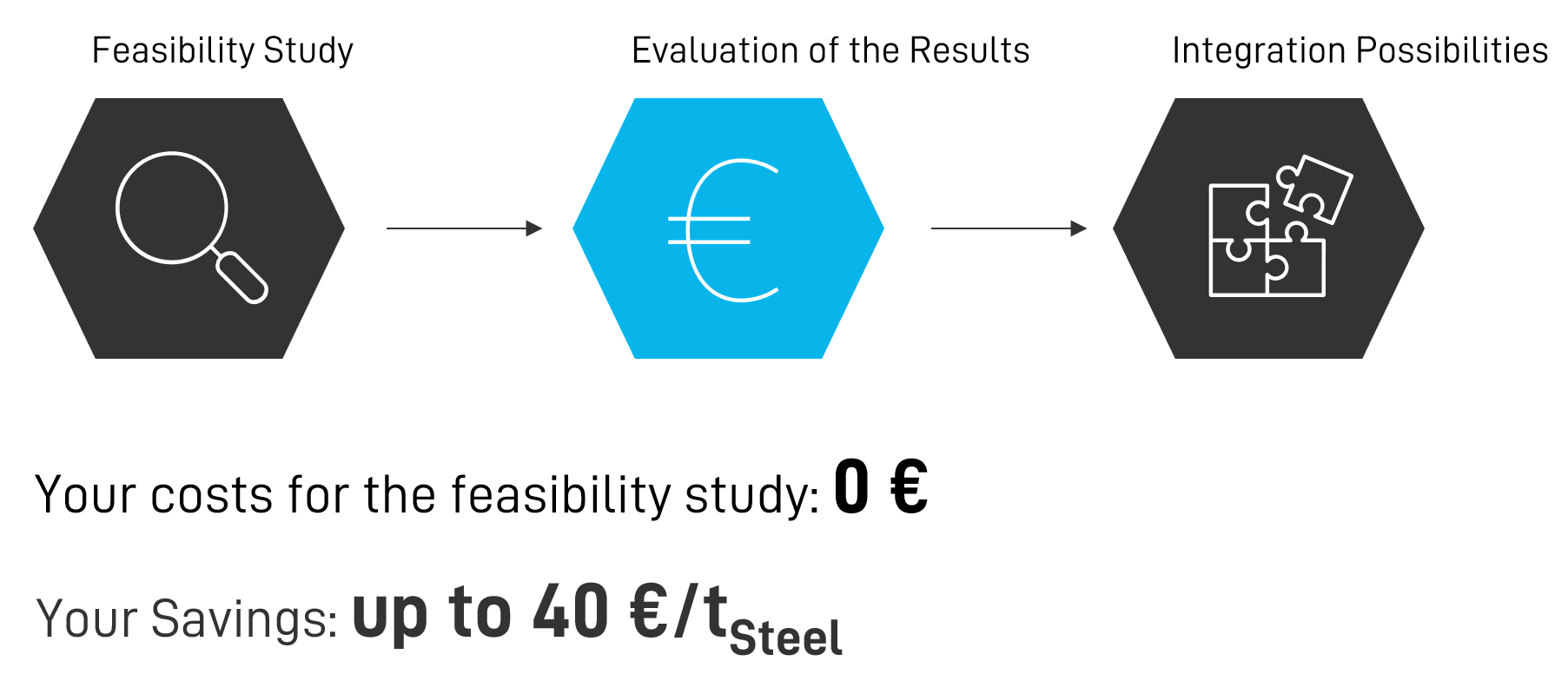
Feasibility Study
Based on input data transmitted to qoncept regarding available raw materials and 3 selected grades the possible costs savings can be evaluated.
Evaluation of the Results
We are presenting and discussing the results with your experts. The raw material costs will be compared with the current costs in order to show the potential savings.
Integration Possibilities
We are presenting the possibilities for a quick and easy integration, the different levels of integration as well as the integration strategy.
Raw materials are the main emission & cost source in steelmaking
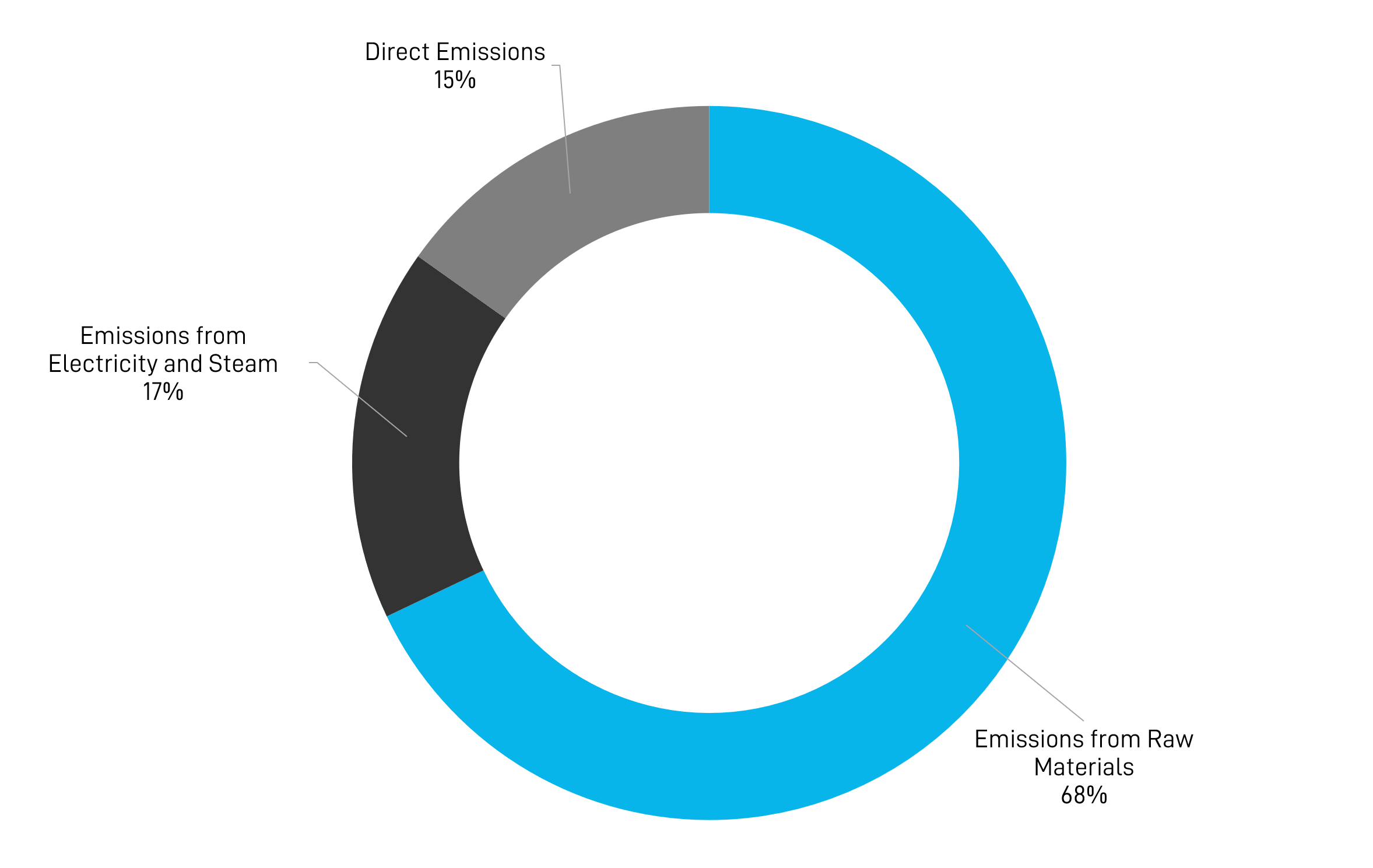
Particularly in the production of high-alloy and stainless steels, the raw material costs can amount to up to 80 % of the total production costs. Furthermore, as illustrated in the figure, 68 % of CO2 emissions in stainless steelmaking arise from raw materials.
Over the past decade, steelmakers have implemented the following two strategies to successfully reduce CO2 emissions:
- Switch from primary steelmaking (blast furnace) to recycling (electric arc furnace)
- Increase the recycling rate of steel scrap in electric arc furnaces
Thus, optimizing the raw material input not only significantly reduces the manuThis facts results in an enormous potential for a significant reduction in raw material costs.Thus, not...
The solution for substantial cost savings and CO2 reduction
Did you know that the growth in the use of stainless steel has been the highest of any material in the world 51 million tons of stainless steel are produced worldwide every year, but this also results 150 million tons of CO2 (Source: ISSF, 2015).
The raw material optimizer helps to lowers the raw material costs as well as the CO2 emissions by determining the best possible choice of raw materials for a specific production route without the need of high CAPEX investments.
The optimizer is based on sophisticated mathematical algorithms in combination with user-friendly softwrae interfaces (GUI), which allow easy to define boundary conditions and constraints.
Based on an in-depth understanding of metallurgical reactions and processes, the algorithm of the software application were further developed in order to enable a process-related, multi-level optimization for the melting and all secondary metallurgy processes.
This enables enormous cost savings of up to 40 €/t.
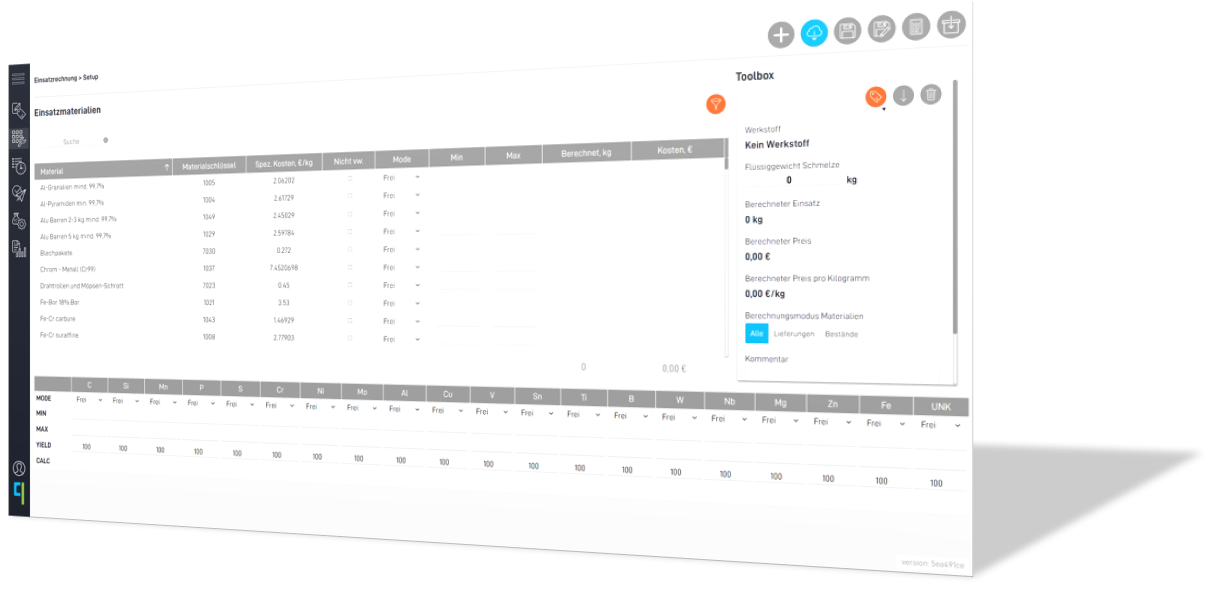
How can such significant cost savings be achieved?
The raw material optimizer is an interdisciplinary development by mathematicians, software engineers and metallurgists. This resulted in a software solution with the following important features to make steelmaking more efficient:
- Metallurgical intelligence inside
- Sophisticated mathematical algorithms enable optimization along the entire steelmaking route
- Current stock and future delieveries can be considered
- The solution enables campaign calculations