computational metallurgy
We pour metallurgical processes into mathematical algorithms.
Steelmaking and Algorithms
Holistic optimization of metallurgical processes
Our computational metallurgy applications are intelligent software solutions in the field of metallurgical process modeling. These process models map the different sub-processes of steelmaking using a holistic approach to optimize the entire production process and support decision-making.
Primary and secondary metallurgy
The model core for EAF, BOF and all secondary metallurgical processes is based on a fundamental and holistic approach, in which the fundamental equations of thermophysics, thermodynamics, reaction kinetics and all energy and mass balances are used within a generally applicable approach. Process-relevant phenomena are integrated as sub-models and their interactions with the holistic and cross-process approach are taken into account.
The developed mathematical algorithm enables the simultaneous release of coupled reactions, taking into account phenomenological events. The structure of the holistic modeling approach follows the concept of model blocks. The macromodels represent the core of the modeling and describe the most important basic aspects of metallurgy, such as thermodynamics and kinetics. Micromodels describe basic phenomena and/or model parameters that are required by the macromodels (for example, the calculation of slag activity or kinetic model parameters). These can be model parameters, empirical/phenomenological described phenomena or highly complex mathematical approaches. Submodels describe plant/process-specific phenomena.
When to contact us
Our metallurgical models feature the following benefits
- Quality improvement
- Prediction of quality-relevant properties
- Early detection and analysis of quality problems
- Improvement of treatment instructions (recipes) and set-points
- Increase in production and performance
- Reduction of process variability
- Improved management and administration of warranty claims
Our metallurgical models can be used in different implementation levels as an offline application or fully integrated to perform real-time calculations. Typical application examples are as follows:
- Integrating metallurgical models into the existing automation system for real-time calculations
- Using the metallurgical models via an offline application to conduct process parameter variations
- Integrating metallurgical models for the entire production route to holistically optimize the value-added chain
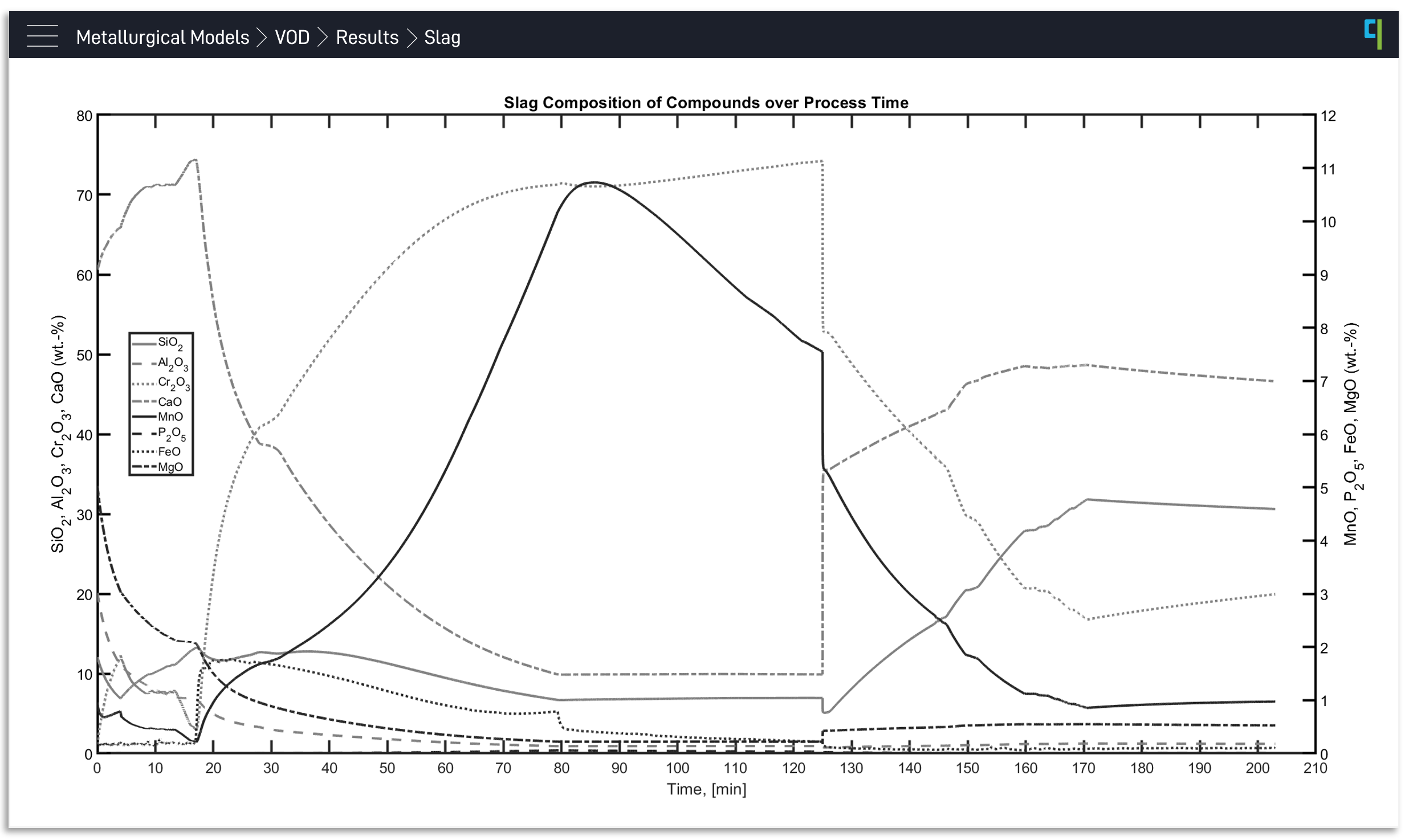
Solidification processes
We can look back on over 20 years of experience in experimental and model-based solidification analysis. In order to be able to analyze and calculate the solidification processes, regardless of process conditions (ingot casting, continuous casting, sand casting), a wide variety of phenomena, from micro- to macroscopic orders of magnitude, must be understood. With our metallurgical understanding of these different phenomena and our competence in numerical simulation and practical experience, we deliver intelligent applications, comprehensive analyses and concepts in the design phase of solidification processes, and process models for integration into existing systems.
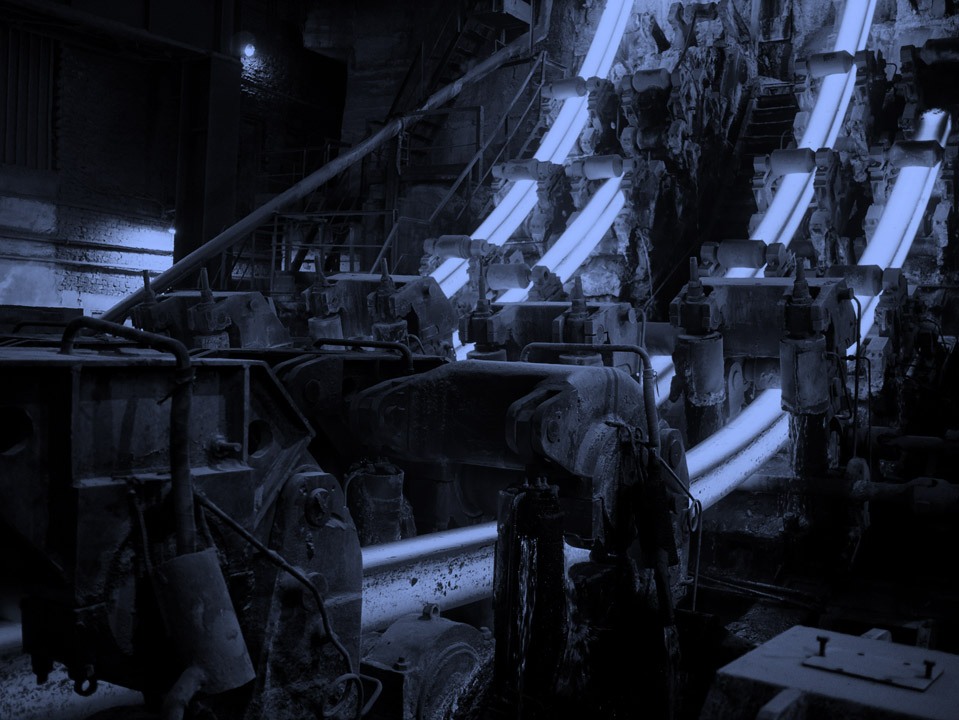
Continuous casting
Computational Casting Analysis services provide a comprehensive analysis of the dedicated states in the continuous casting. Our solution makes use of numerical algorithms and models to compute the thermo-physical fundamentals that occur during the continuous casting process.
When to contact us
A comprehensive analysis of the dedicated states in the continuous casting process from a technologically oriented, metallurgical approach is essential for the following metallurgical interpretations:
- Understanding the temperature distribution on the strand surface and selected positions inside the cast strand.
- Understanding the shell growth for selected fractions of solid during the whole casting process.
- Determining the point of total solidification.
- Determination of optimal positioning of technological devices such as the following:
- Strand electro-magnetic stirrer
- Final electro-magnetic stirrers
- Mechanical or thermal soft-reduction
- Soft-cooling tunnels
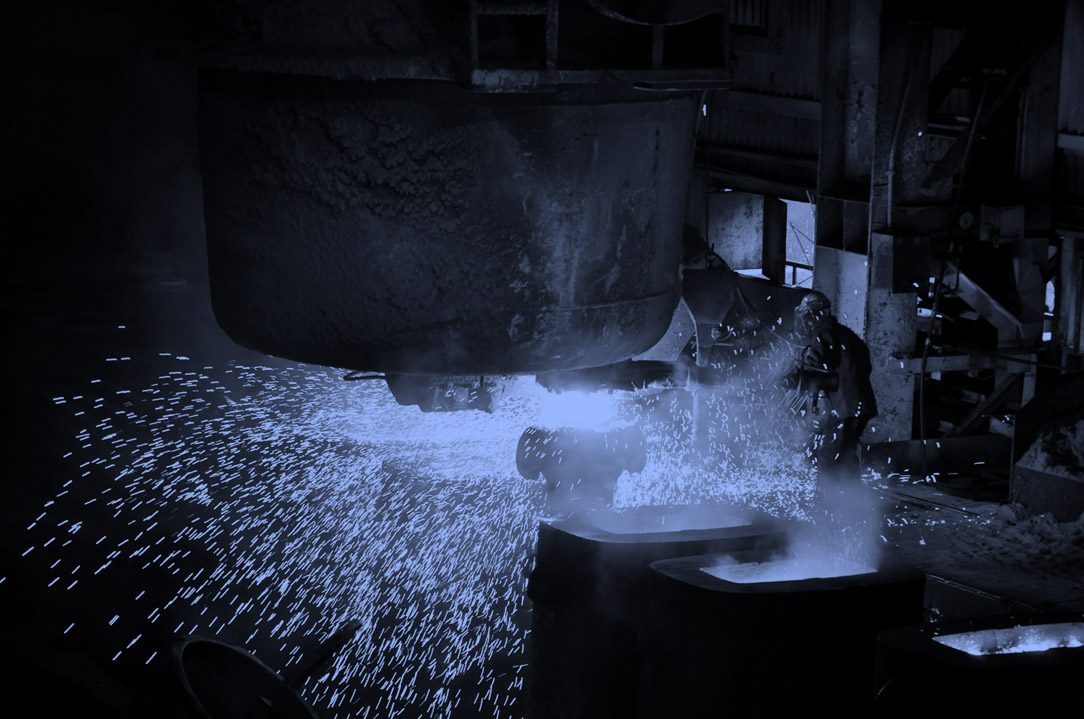
Ingot casting
Ingot casting is of fundamental importance for the production of many steel grades, especially for the production of ingots for forging. The complex phenomena during this process must be controlled in order to maintain a good quality for the final product. The optimal casting parameters in ingot casting exist in a multi-dimensional relationship to each other. The casting speed not only depends on the ingot format but must also be defined as a function of the steel analysis, the superheat and the casting sequence. Other important casting parameters include the type and quantity of the casting powder, the exothermic powder and the covering powder.
When to contact us
The numerical simulation can be a highly efficient application for the following:
- Optimizing mold geometry and the entire casting set (funnels, plates, channels and hot tops)
- Optimizing casting parameters
- Minimizing pores, porosity and segregation
Thermophysical material data
Profound and well verified material data are the basis for proper solidification analyses. Accordingly, qoncept developed a sub-model to calculate temperature-dependent thermophysical properties of steels (or other metals) which are required by the numerical model. These data are specifically calculated for each material, depending on the exact chemical composition.
In addition, the relationship between temperature and phase fractions is calculated by a microsegregation model, which in turn takes into account the specific chemical composition of the material and the cooling rate.
The following two figures show the quasi-binary Fe-C diagram in a non-equilibrium state (cooling rate = 1 °C/s) for 0 wt.-% Mn (left figure) and 2.0 wt.-% Mn (right figure). The blue vertical line corresponds to an alloy with 0.16 wt.-% carbon. It can clearly be seen how the increasing manganese content, which narrows the δ-ferrite region, shifts the liquidus solidus and the peritectic transformation to lower temperatures. Additionally, the points CA, CB and CC are shifted to smaller carbon contents. Thus, in the case of 0 wt.-% Mn, a steel grade with 0.16 wt.-%C is between CA and CB, whereas the same grade with 2 wt.-% Mn is already to the right of CB. This has a significant influence on the solidification behavior in both continuous casting and ingot casting.
The figures below show the typical characteristics of thermophysical data, such as density, heat capacity and thermal conductivity. The transformation points, which occur from the solidification and the subsequent cooling down to room temperatures, are easily perceived.
When to contact us
We offer the possibility of calculating the thermophysical properties for specific steel grades in different models:
- Latent heat as a function of chemical composition
- Specific heat capacity (or enthalpy) as a function of temperature and chemical composition
- Density as a function of temperature and chemical composition
- Heat conductivity as a function of temperature and chemical composition
- Phase fractions (liquid or solid fraction) as a function of temperature and chemical composition